Metric O Ring Face Seal Groove Design History Of The Iso 3601 Series Of Standards For O Rings Fluid As568b Standard O Ring Groove Design Seal Design Inc O Ring Groove Design O Ring Groove Dimensions Mykin Inc Groove Design Gland Design O Ring Groove Gland Design O Ring Seals For Dynamic ApplicationsDovetail grooves are used to hold the Oring in place during installation or maintenance This groove design is relatively uncommon as it is expensive to machine and should not be used unless absolutely required The dovetail groove construction is only recommended for Orings with cross sections of 139 inch (3,53 mm) and largerIf you are designing a face seal, select the ORing with an inside diameter which will position the ORing on the side of the groove opposite the pressure Click here for more information on face seal groove design Note the ORing inside diameter for the next step Calculate the Seal Stretch Using Equation 1, calculate the installed seal stretch
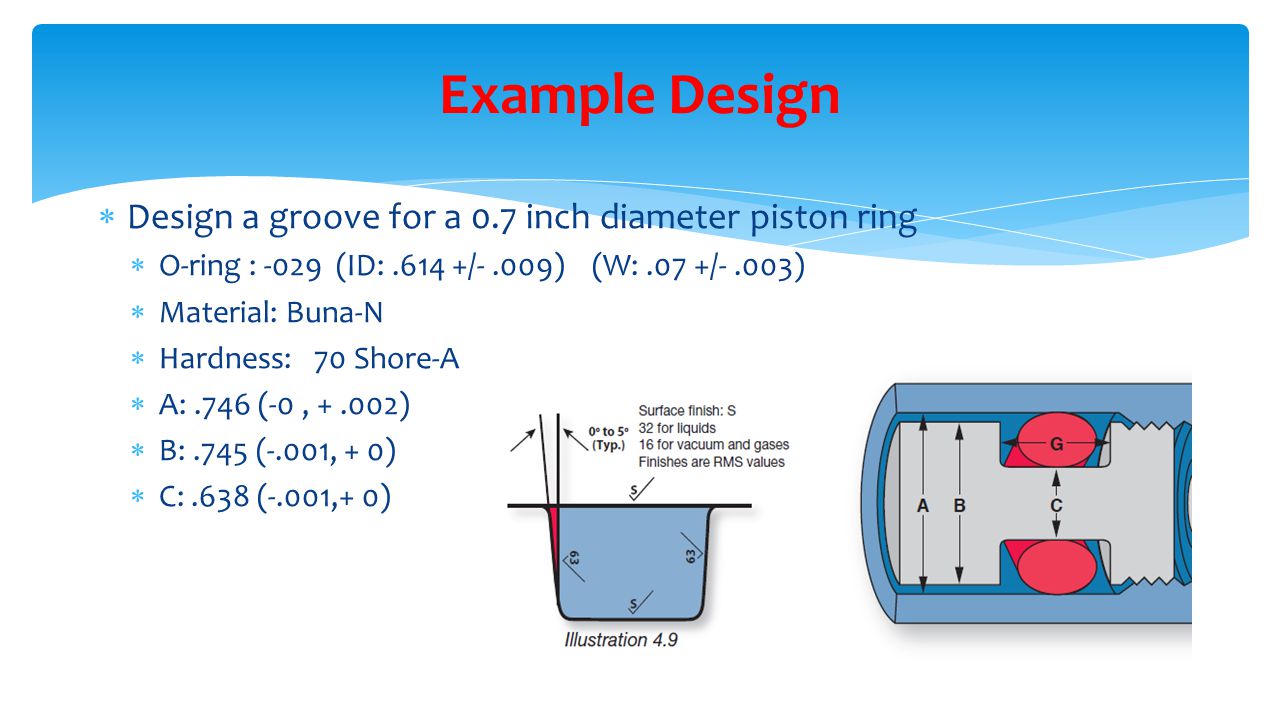
Design Of O Ring Seals Ppt Video Online Download
O-ring groove design face seal
O-ring groove design face seal-AS568B CS Depth Inches % Liquids Gases Radius004 to050Did you get a defective seal?
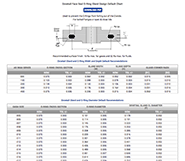



O Ring Groove Design Guides Engineering Quick Reference
30/7/21 But some sacrifice must be made in the pressure limitations of the seal and also in the life of the sealFor a bore (piston) seal QuadRing® Brand Groove Diameter = Max Bore Diameter – (2 X Recommended Gland Depth) For a face seal QuadRing® Brand Groove Depth = Recommended Gland Depth – Application Clearance With a face seal, if the two surfaces to be sealed are inO Ring Groove Design Standard Dovetail grooves are used to hold the Oring inplace on a face seal groove during during assembly and maintenance of equipment An undercut or dovetail groove has proven beneficial in many applications to keep the oring in placeSure act on the Oring in the same direction Groove design can reduce the tendency for extrusion See figures 132 a & b If the friction of the moving metal surface across the Oring is in the same direction as the direction of the pressure, the Oring will be dragged into the clearance gap more readily and thus extrude at about 35% of the
ORing Groove Design 1 The following sizes are not normally recommended for dynamic service, although special applications may permit their use 2 Clearances shown are based on 70 durometer materials The clearances must be held to an absolute minimum consistent with design requirements for temperature variations and should not exceed theDovetail ORing Gland Design In a dovetail oring gland application the oring squeeze is primarily axial in direction, where a valve exerts force on the top and bottom of the orings surfaces Typically used in static or slow moving applications the dovetail orings gland purpose is to properly hold the oring in place during machine operationStatic ORing Groove Design Face Seal
Face seals are often located in a groove or cavity on a flange A gasket (orange) used as a face seal to prevent flow from escaping from a pipe flange joint ISO 8434 specifies the general and dimensional requirements for the design and performance of Oring face seal connectors made of steel for tube outside diameters or hose inside diameters of 6 mm through 38 mm, inclusiveGroove volume, oring inner diameter stretch and even much more The ERIKS Oring design calculator features the calculation of Oring Gland Design Dovetail seal Also here there is a metal to metal contact as long as the construction will notThe face seal design chart below explains the hardware dimensions to use for an Oring seal when the groove is cut into a flat surface For designing systems which contain internal pressure, like the example below, the groove's outside diameter (OD) is primary, and the groove's width then determines the inside diameter
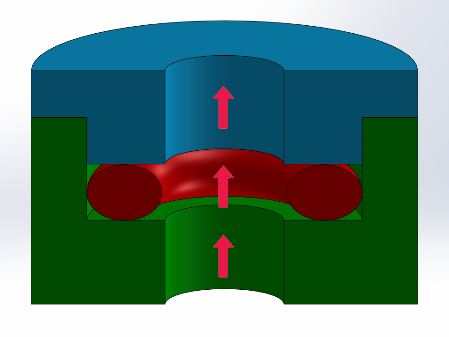



4 Common Mistakes In Designing For An O Ring Axial Face Seal Hot Topics




Oring Ehandbook
Face seals need a consistent pressure around the entire oring to create a seal, but their groove diameters are not especially critical Face seals are a simple oring gland design and most adaptable to imprecise geometries, but require precise and solid attachment and checking over timeThe groove OD is calculated by adding twice the appropriate groove width The recommended gland depths for QuadRing® Brand seal and ORing face seal applications are the same as for radial applications Recommended gland depths can be found in the QuadRing® Brand seal tables and for an ORingORing Groove Design Guides Expert Application Engineering Assistance Oring groove design guides offer default dimensional guidance on the most basic oring groove design applications The best orings are useless without the right groove design which becomes increasingly important the more demanding the application environment




How To Design An O Ring Groove Vizeng




O Ring Groove Design
DOVETAIL GROOVE DESIGN Dovetail grooves are used to hold the Oring inplace on a face seal groove during during assembly and maintenance of equipment An undercut or dovetail groove has proven beneficial in many applications to keep the oring in placeOring crosssection oring diameter dovetail gland cl diameter (f) nom tol / nom tol / nom tol /dovetail gland and oring width and depth default recommendations dovetail gland and oring diameter default recommendations005 0070 0003 0101 0005 0178 0070 0003 0114 0005 0191 0070 0003 0145 0005 0222 0002WwwparkeroringscomInstalling an Oring in a face seal gland is among the easiest of all installations However, that doesn't mean that there's not potentia



Static Axial Internal Pressure Gland Groove Design



Http Practicalmaintenance Net Wp Content Uploads Working Design Considerations And Maintenance Of O Rings Pdf
Gland Design for Static Application for Orings with Axial Squeeze Surface Finish X groove top and bottom for liquids X = 32 micro inches (08 μm Ra) • Gland Dimensions Static ApplicationFace Seal GlandsMetric W Oring Cross Section E Gland Depth FXRing Sizing Charts USA XRing Size Chart;Be it dynamic or static operation, radial or axial loading, vacuum or high pressure




O Ring Groove Dimensions Calculator Precision Polymer Engineering




O Rings An Overview Sciencedirect Topics
ORing Inside dia (mm 4 digits 1 decimal place)"" O Ring Section (mm 2 digits 1 decimal place) with the decimal point excluded For example is an Oring of 545mm ID with 30 mm section Surface Texture The surface texture of the surfaces in contact with the Oring seals should not exceedORing Design Considerations What to Know About ORing Squeeze, Stretch, Compression, and More Our oring groove design guides list default oring groove dimensions for the most basic applications and are intended to be used with the following oring groove design considerations to engineer on oring gland to optimize specific application performance2/3/16 O Ring Groove Design Face Seal Hi Guys Beautiful Design, On this occasion we gave several images / wallpapers related to the title O Ring Groove Design Face Seal, you can download it for reference or collectionAlright, happy reading Title O Ring Groove Design Face Seal link O Ring Groove Design Face Seal




Engineering Basics Guide To O Rings Eriks Shop Nl




Oring Ehandbook
ERIKS standard ORings and load them also into your created design info chemical volume swell (%) cross section diameter (mm) ISO 3601 free Calculate Results Reset calculatorDOVETAIL ORING GROOVE DESIGN Dovetail grooves are used to hold the Oring inplace on a face seal groove during during assembly and maintenance of equipment An undercut or dovetail groove has proven beneficial in many applications to keep the oring in place This is an expensive groove to machine, however, and thus should be usedO'ring Groove Design As important as the o'ring seal itself is the groove that the o'ring seats into The groove must be designed to accommodate not just the o'ring size, but also its intended usage;
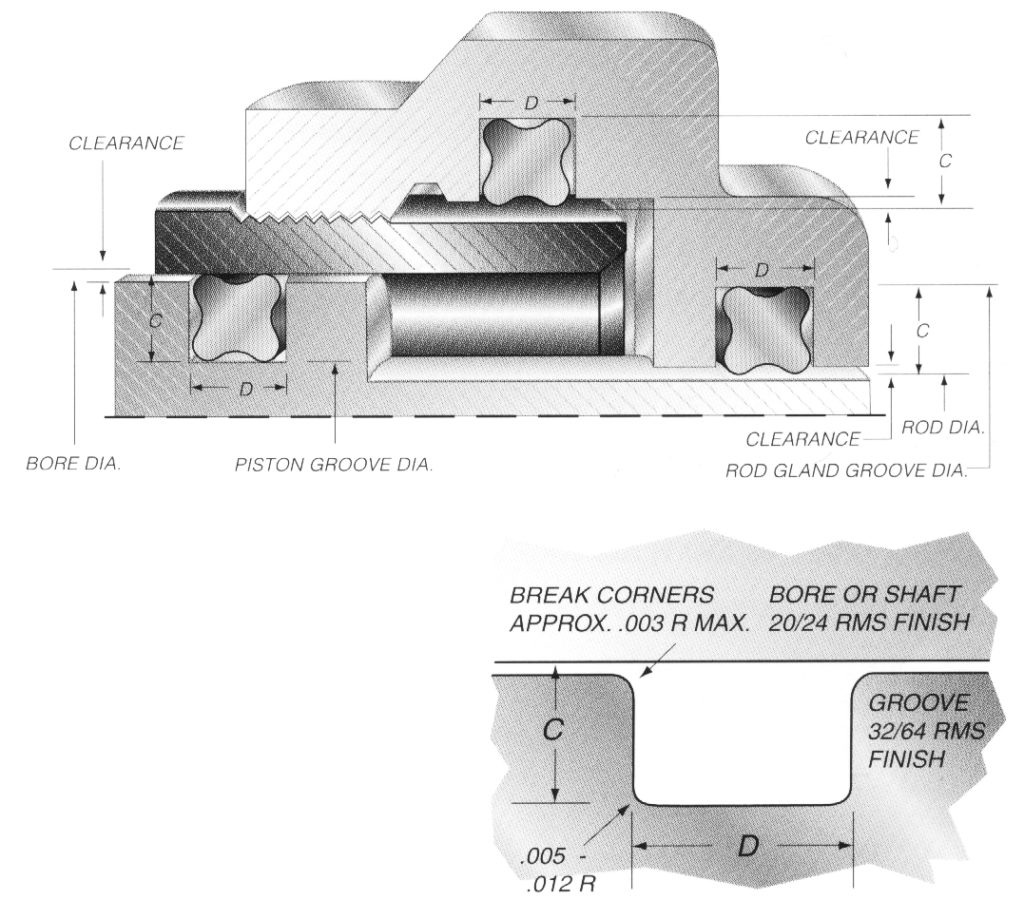



Quad Ring Groove Design Daemar Inc
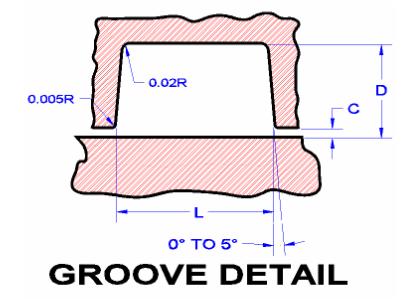



Seals Eastern O Ring Rod Seal Design Guideline
In a static axial seal application the squeeze is on both the top and bottom of the orings cross section Static axial seals are typically used in face seal applications The table below lists recommended dimensions for static axial (internal pressure) seal glands by AS568 oring dash numbers Static Radial GlandsMechanical / Heavy Duty Face Seals 'O' Ring Kits Circlip Kits Splicing Kits 'O' Ring Cord BARNWELL 'O' RINGS 3 BARNWELL must be incorporated in the design resulting in wider grooves If these factors are not known, you effect a seal in a groove size of almost equal volume It is BARNWELL 'O' RINGS 4 The 'O' Ring Picture this You have an application using a standard ORing The ORing seals great, but is wearing out very quickly, and friction is far exceeding the goals of the system You retrofit a fancy PTFE spring energized seal that costs 1000 times more than the ORingonly to find out it leaks!



1
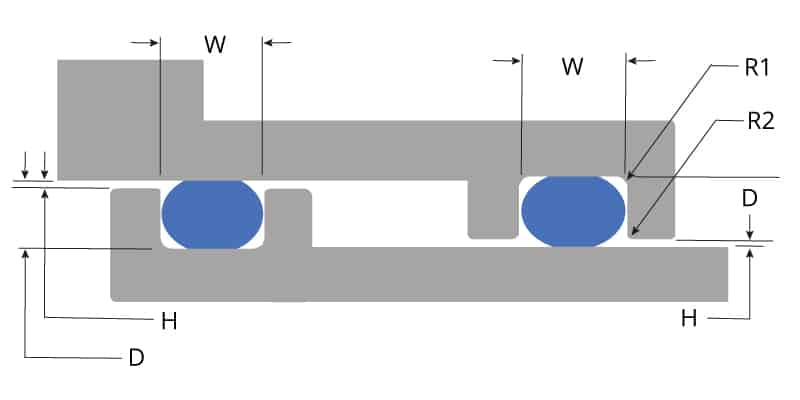



O Ring Groove Design Global O Ring And Seal
The groove design allows the Oring to be retained in the face seal during assembly and maintenance This is beneficial for special applications where the Oring has to be fixed by the groove eg a lid which opens regularly Bosstail The Oring is used for sealing straight thread tube fittings in a bossStandard Groove Design Orings can be used in components in a wide variety of ways During the design stage installation must be taken into consideration In order to avoid damage during installation it should not be necessary to pass the Oring over edges or bores When long sliding movements are involved, the seal seat should be recessed, ifThe Oring calculator tool is intended to form the basis of an oring installation, and assist with selection of oring and hardware dimensions Recommendations are based on available technical information, and are offered as suggestions only, any reliance placed on such information by the user is strictly at the user's risk




Standard Dovetail Grooves Dovetail Groove Engineering Design Guide




O Ring Groove Design Standard As568b Seal Design Inc
Oring is "the fi nest static seal ever developed" 41 Surface Finish for Static ORing Seals The design charts indicate a surface roughness value not to exceed 32 microinches (32 rms) on the sealing surfaces for static seals with a maximum of 16 rms recommended for facetype gas seals These fi gures are good general guidelines,ORing Groove Design Reference Guides utilize the same defaults as ORings and adjusted to maximize application performance ORing Groove Design Guides ORing Gland Design Considerations;If you are designing a face seal, select the QuadRing® Brand with an inside diameter which will position the QuadRing® Brand on the side of the groove opposite the pressure Click here for more information on face seal groove design Note the QuadRing® Brand inside diameter for the next step Calculate the Seal Stretch




O Ring Groove Dimensions Calculator Precision Polymer Engineering
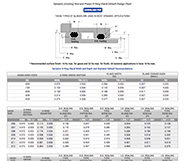



O Ring Groove Design Guides Engineering Quick Reference
Oring Groove Design in 3 easy steps Step 1 Choose whether you are working with existing hardware or designing new hardware Select the type of Oring groove piston, rod, face seal or trapped seal If the Oring size required is known, simply select the AS, BS or ISO standard (such as AS568) and enter the dash size referenceORing Face Seal Glands These dimensions are intended primarily for face type Oring seals and low temperature applications ORing Size Parker No 2 W Cross Section Nominal Actual L Gland Depth Squeeze Actual % G Groove Width R Groove Liquids Radius Vacuum and Gases 004 through 050 1/ ±003 (178 mm)050 to to023 19 toRubber Seals, Sealing Devices & ORing Seal Design Apple




O Ring Groove Design Sealing Australia



Untitled Document
Tested in face type Oring seals using grooves that provided 15%, 30% and 50% compression For vertical Oring applications (as a chamber), it is desirable to use an undercut groove similar to that shown in Figure 1 The Oring is held firmly in place and has no tendency to drop out of the groove when the chamber is open Figure 1Grooves for Static vs Dynamic Seals A Static seal grooves are normally designed to have Between 15%25% squeeze on the ORing Static seals can tolerate higher volume swell of the O Ring than dynamic sealsGroove Design Technical Data Static ORing Axial (Face Seal) Glands Gland Squeeze Groove Width Groove;




Advantages Of A Quad Ring Over An O Ring
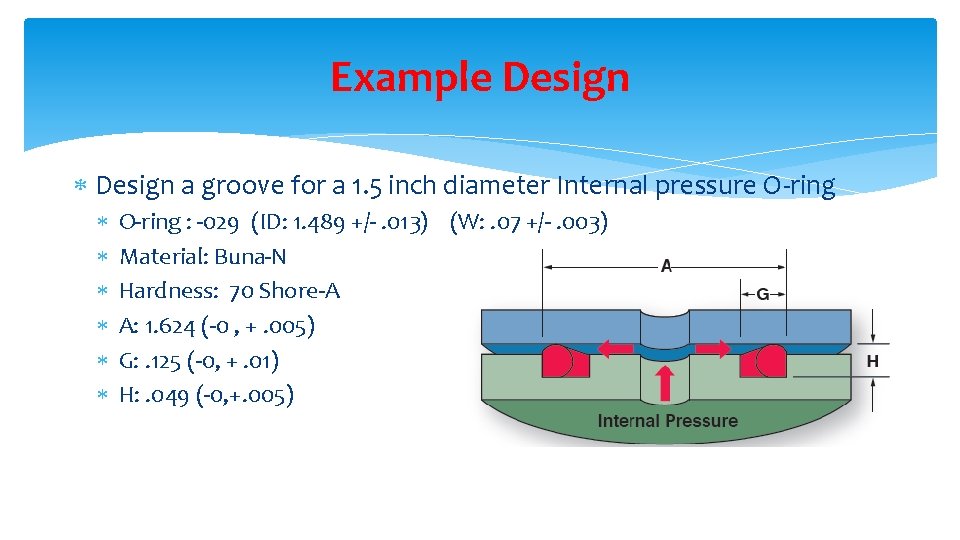



Design Of Oring Seals Design Of Oring Seals
24/9/16 Sealing Fundamentals Face Seal The physics of creating a face seal is relatively simple In most sealing systems, the objective is to prevent fluid from leaking from a highpressure location to a lower pressure location through a sealing gap Sealing fundamentals should be followed for trouble free application7/6/17 A noncircular face seal footprint might also be called a racetrack groove, a wandering groove or a custom plan view When using an Oring, the main design consideration is the corner or smallest radius (shown "r" in diagram) The inside radius should be at least three times the Oring cross sectional diameter▪ For external pressure face seals, the ID of the Oring should be slightly smaller than the inner diameter (In) so that when the pressure is applied, the Oring is already where it would be as a result of the pressure
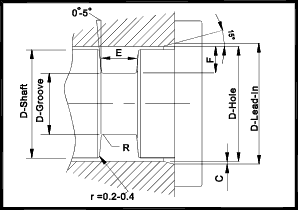



O Ring Seals Roy Mech




Fep O Rings Trelleborg Sealing Solutions
Most oring face seal applications have a groove designed into one of the mating hardware components The geometry of the groove is important – the dimensions need to be specific because the oring is located in the groove One ofAs568b standard oring groove design Contact Us For Assistance Or Samples Click Here and contact us today to receive a quote or if you have any questions regarding sizing × Dismiss alert The three main types of standard groove designs are Industrial Static also called Radial, Industrial Reciprocating also called Dynamic, and Face Seals also called Axial or FlangeSTANDARD AS568B ORING GROOVE DESIGN The three main types of standard groove designs are Industrial Static, also called Radial, Industrial Reciprocating, also called Dynamic, and Face Seals also called Axial or Flange Radial and Dynamic seals require the presence of a diametrical clearance gap for installation




O Ring Groove Design O Ring Groove Dimensions Mykin Inc
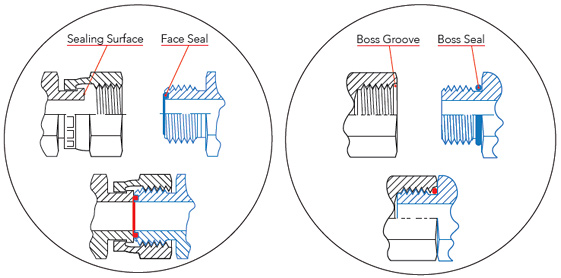



Sealing Methods Adaptall
To find the groove dimensions on a rotating seal, use Design Chart 5 Find the shaft size in the second column The groove root diameter and width will be found under their respective columns The Pressure Seals Oring size will be found in the first column next to the shaft diameter BACKUP RINGS (Design Chart 7)




O Rings Encapsulated O Rings



Www Hitechseals Com Includes Pdf O Ring Brochure Pdf



Untitled Document




How To Design An O Ring Groove Vizeng
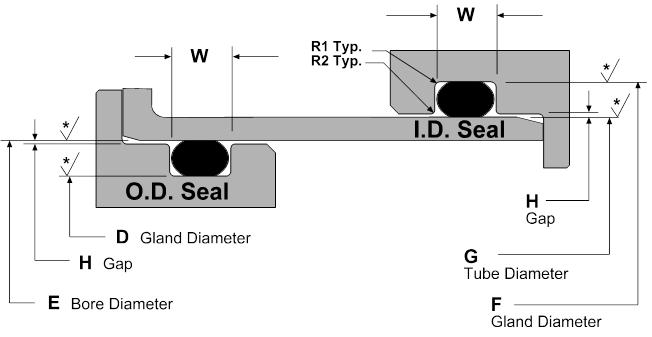



Static O Ring Groove Design A Rod And Piston Glands



Groove Design Gland Design O Ring Groove Gland Design
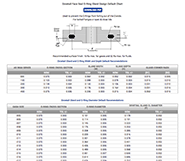



O Ring Groove Design Guides Engineering Quick Reference




Parker S O Ring Selector App Youtube



Groove Design Gland Design O Ring Groove Gland Design
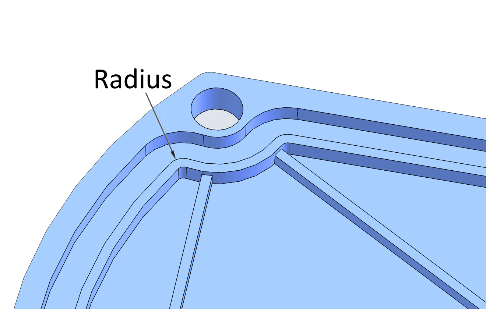



4 Common Mistakes In Designing For An O Ring Axial Face Seal Hot Topics




Design Of Oring Seals Design Of Oring Seals



O Rings What You Need To Know




Great Resource For Designing With O Rings Inventor Tales
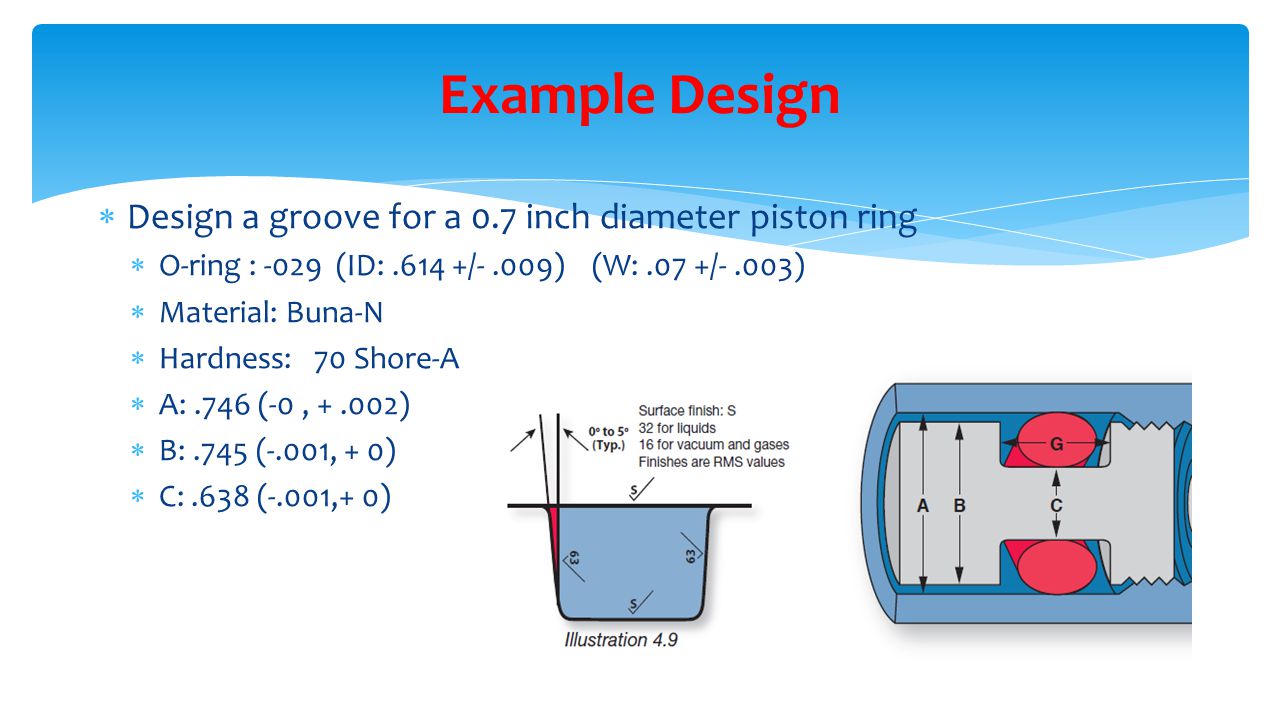



Design Of O Ring Seals Ppt Video Online Download
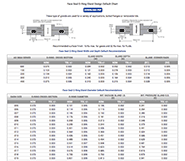



O Ring Groove Design Guides Engineering Quick Reference




O Rings O Yeah How To Select Design And Install O Ring Seals Tarkka
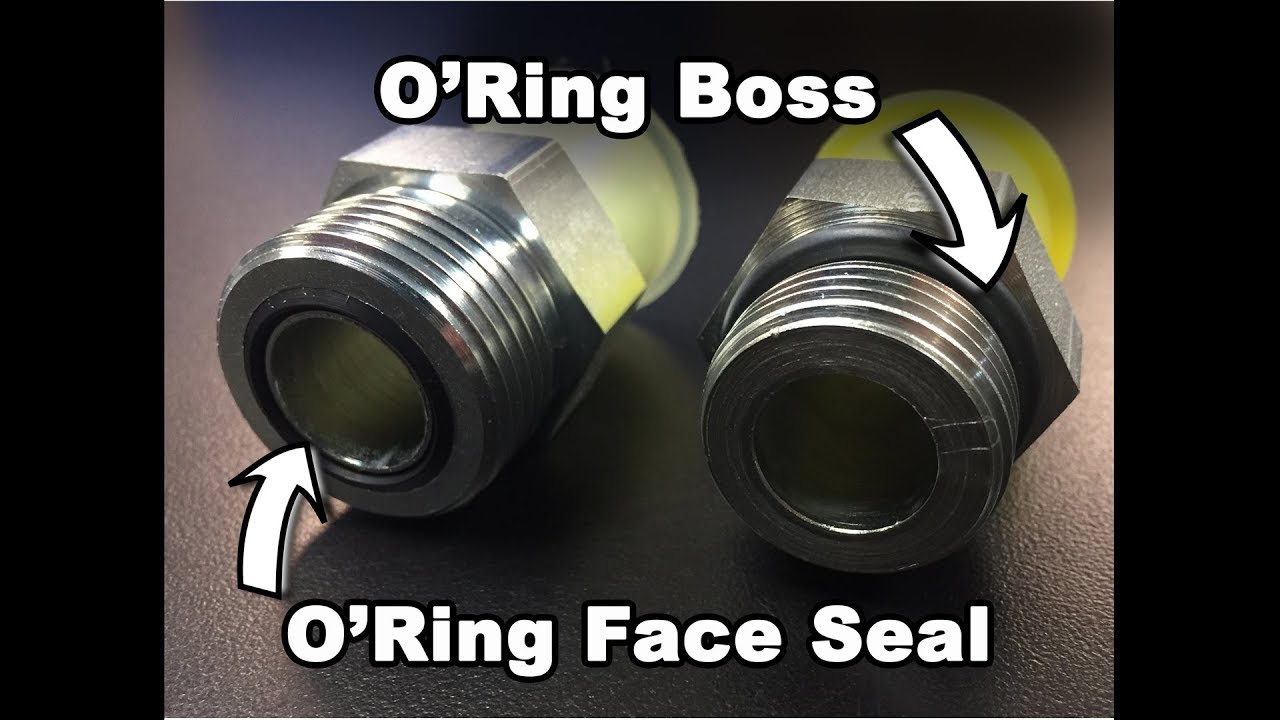



The Different Between O Ring Boss And O Ring Face Sealing Sae Fittings Youtube
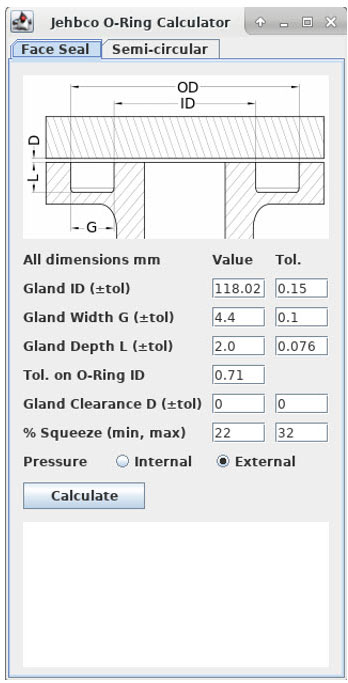



Jehbco S O Ring Design Articles Jehbco Silicones
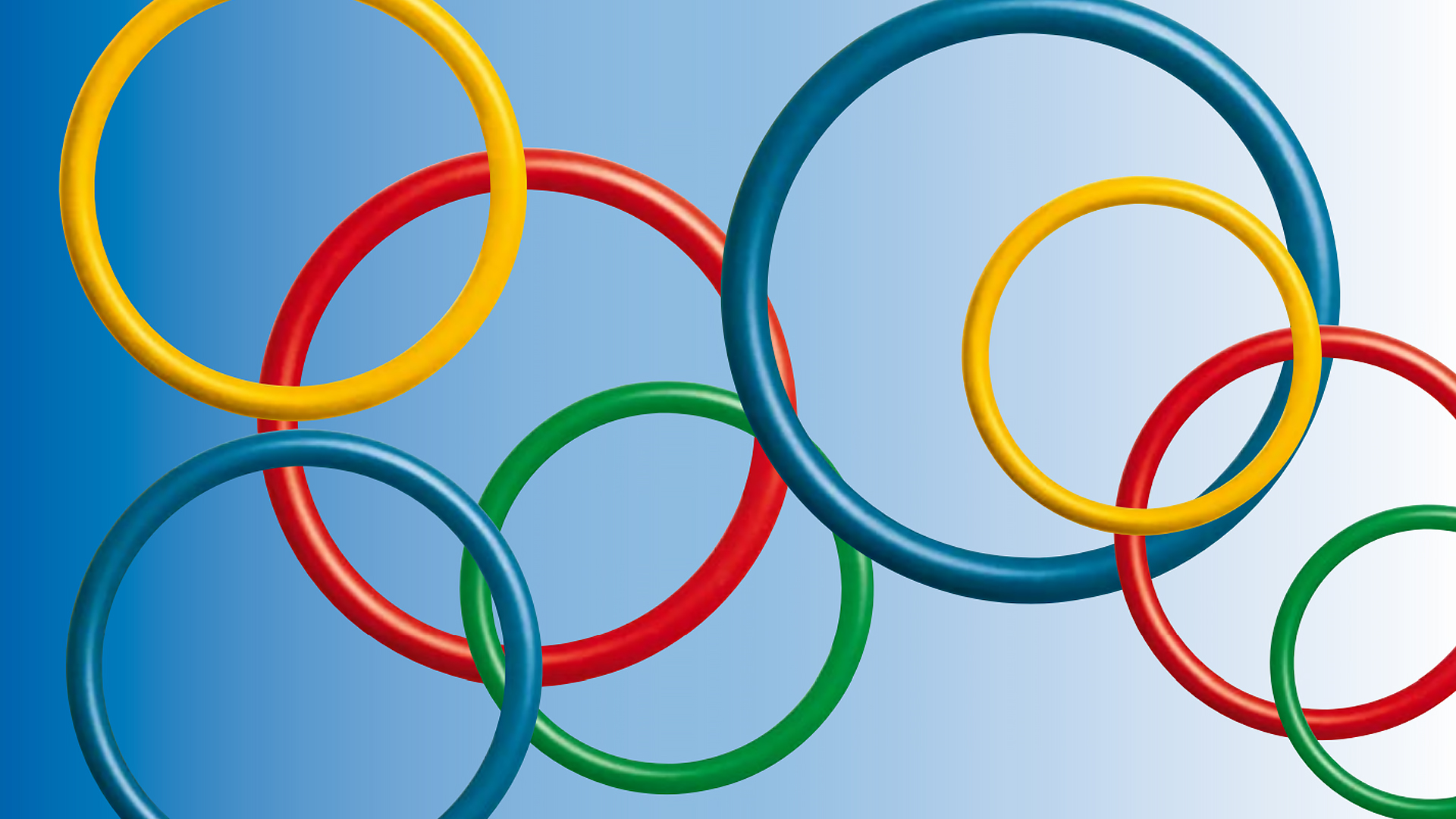



O Ring Groove Calculator O Ring
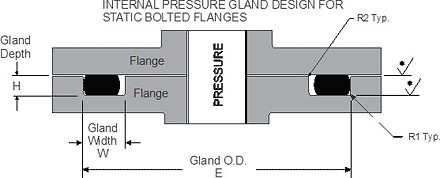



Static O Ring Face Seal Groove Design Guide
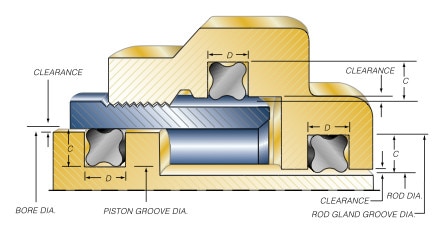



Groove Design Quad Ring Seals Minnesota Rubber Plastics
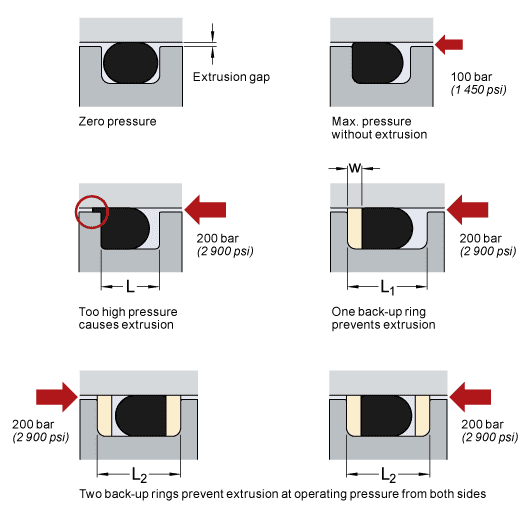



O Rings And Back Up Rings Skf Skf



Designing Axial Static O Ring Grooves To Industry Standards Grabcad Tutorials



Http Www Qualityseals Com Pdfs Groovedesignandoringinstallation Pdf




How To Design An O Ring Groove Vizeng



Newdealseals Com App Uploads 04 Newdealseals O Ring Handbook 14 Pdf




Use And Misuse Of O Rings Normandale Community College
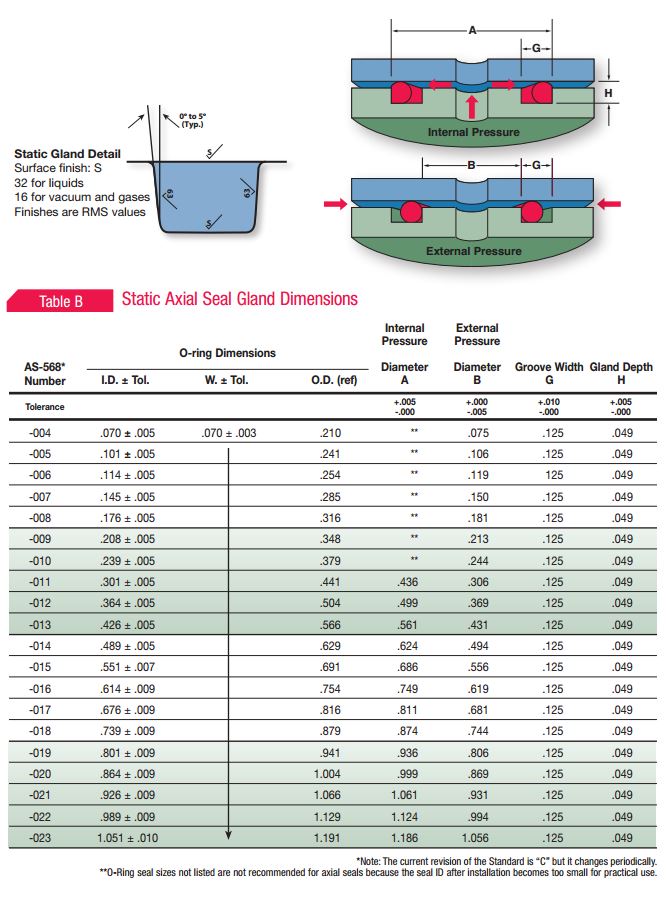



What You Need To Know About Designing Axial Seals Hot Topics




O Ring Wikipedia



1
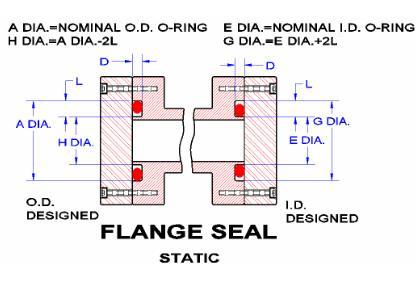



Seals Eastern Flange Seal O Ring Design Guideline



Www Darcoid Com Userfiles Cms Subpage Files 30 Gland Design Pdf



Sae J1453 O Ring Face Seal Groove Size Chart Knowledge Yuyao Jiayuan Hydraulic Fitting Factory
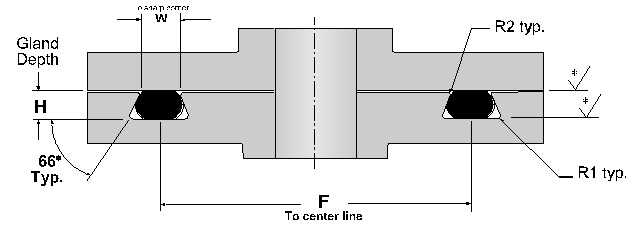



Dovetail O Ring Groove Design Guide A Basic Recommendations




American Seal Packing General Design And Gland Dimensions



Sae J1453 O Ring Face Seal Groove Size Chart Knowledge Yuyao Jiayuan Hydraulic Fitting Factory
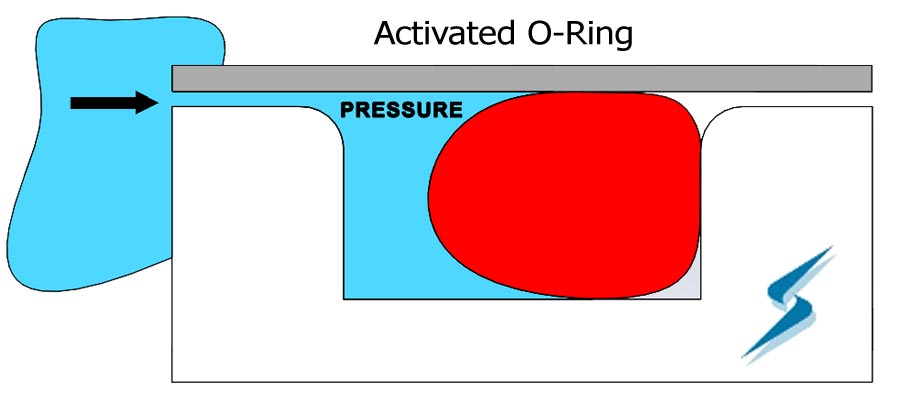



Silicone O Rings Custom O Rings Silicone Seals Stockwell Elastomerics
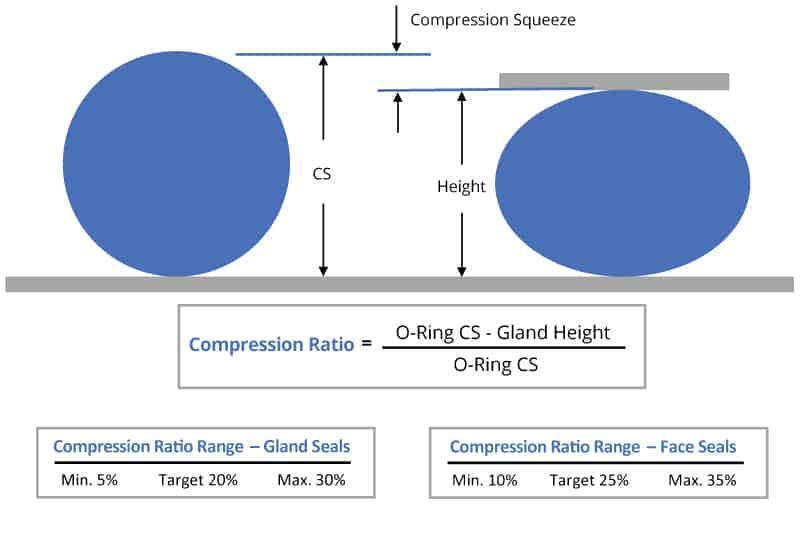



O Ring Groove Design Global O Ring And Seal
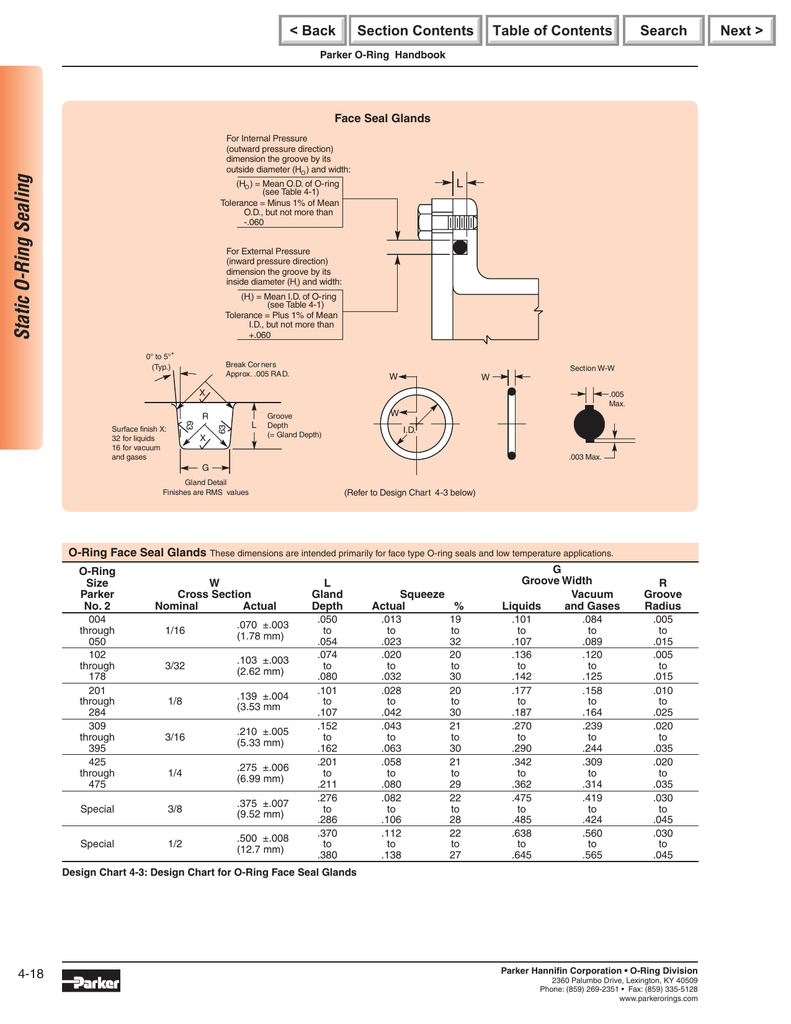



Static O Ring Sealing Sealing Devices Inc
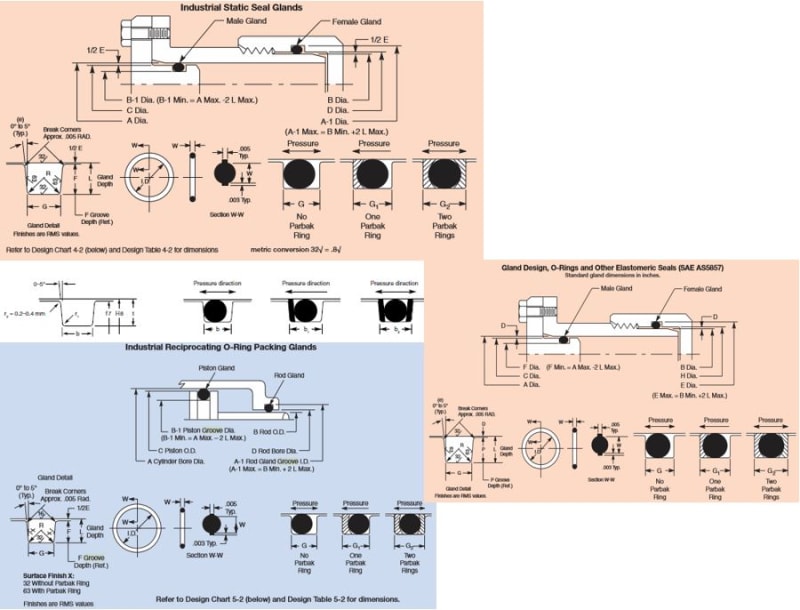



O Ring Groove Drafting Standards Gd T Tolerance Analysis Eng Tips
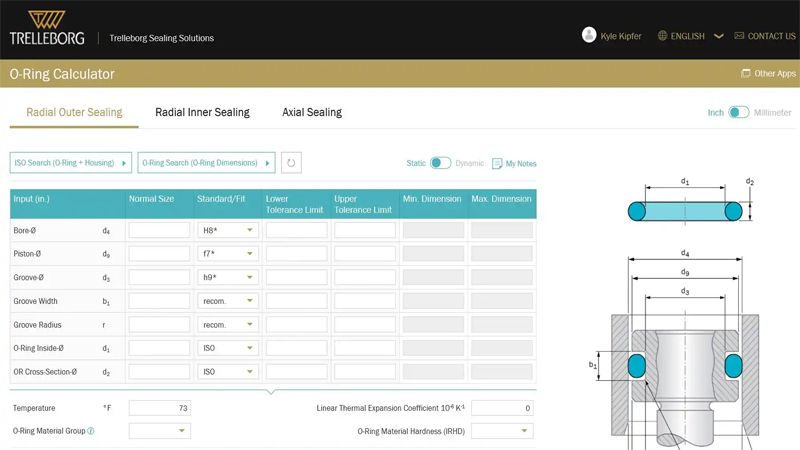



O Ring Calculator Trelleborg Sealing Solutions



O Ring Cross Section O Ring Groove Design Data
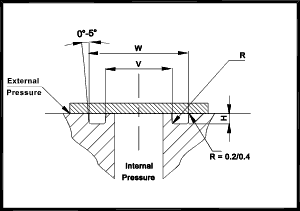



O Ring Seals Roy Mech




2 Design And Detail Information O Rings Stock O Ring Webshop
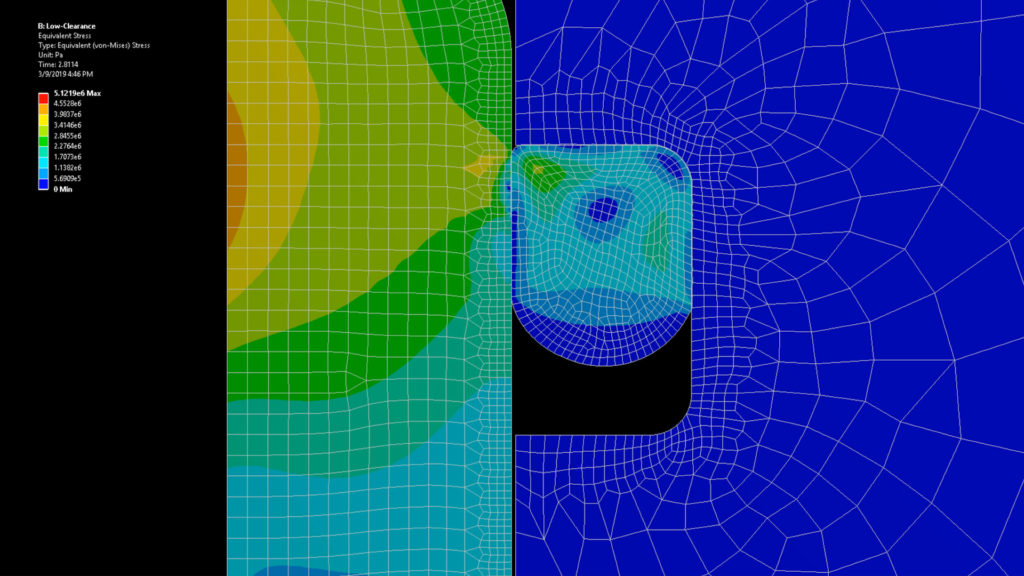



O Rings O Yeah How To Select Design And Install O Ring Seals Tarkka
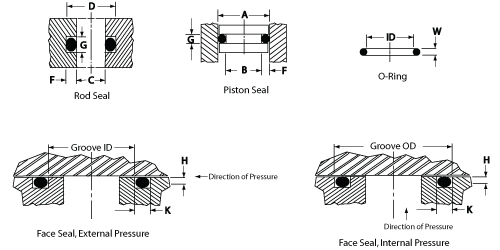



O Ring Groove Design Daemar Inc




O Ring Groove Design Metric Seal Design Inc
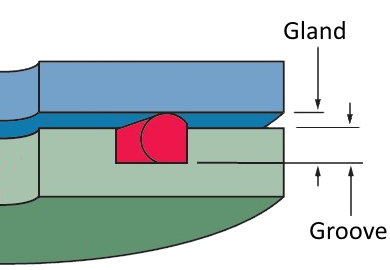



4 Common Mistakes In Designing For An O Ring Axial Face Seal Hot Topics
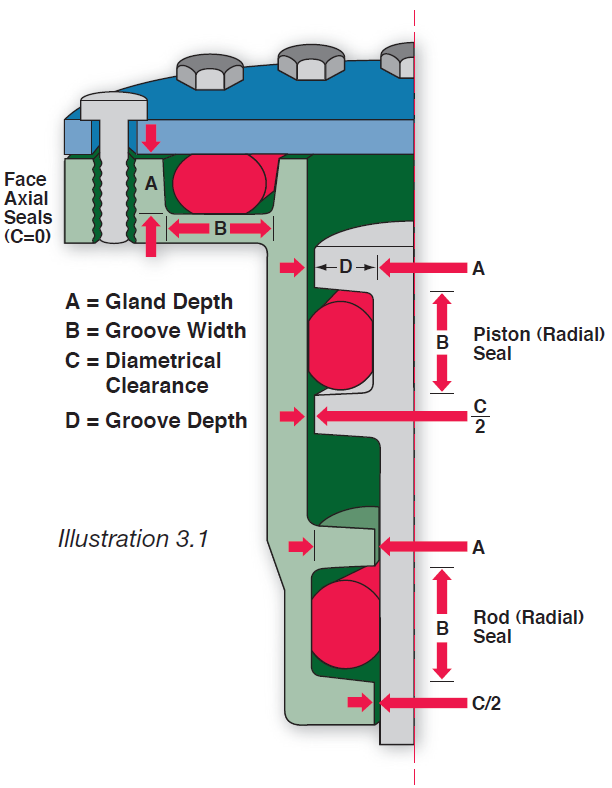



Fundamental Of O Ring




Designing A Non Circular Radial O Ring Seal Engineering Stack Exchange
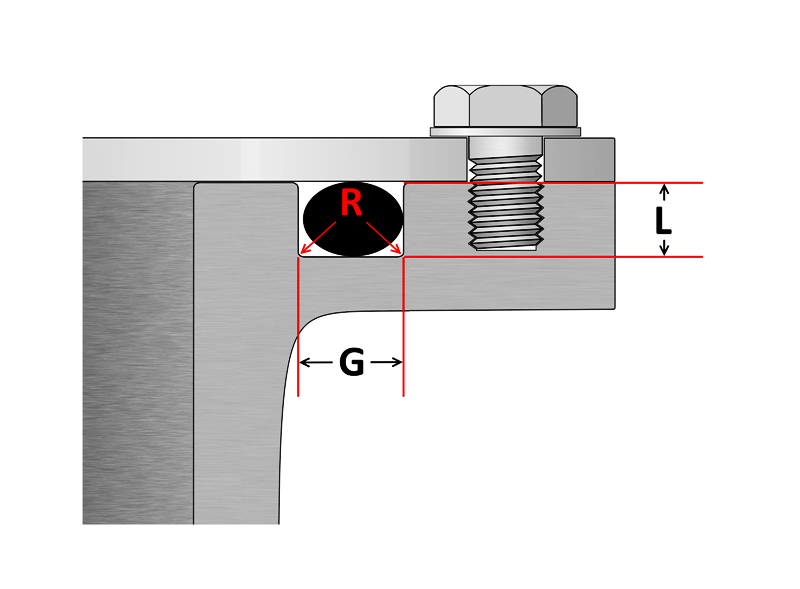



O Ring Groove Design Sealing Australia




O Ring Groove Design Sealing Australia




E S Electronic Service Gmbh Racetrack Grooves Can O Rings Be Used In Non Circular Groove Patterns
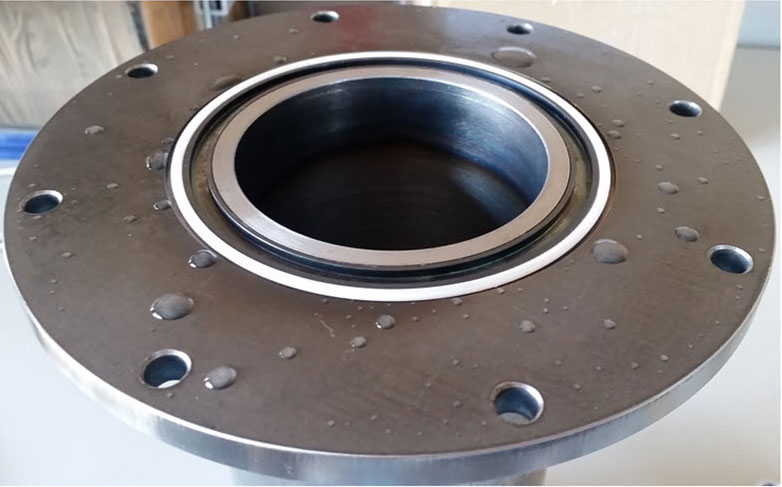



Jehbco S O Ring Design Articles Jehbco Silicones
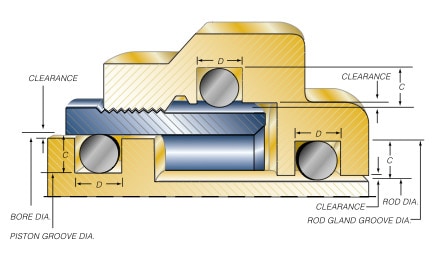



Groove Design O Ring Seals Minnesota Rubber Plastics




Back Up Rings O Rings Performance Sealing Inc
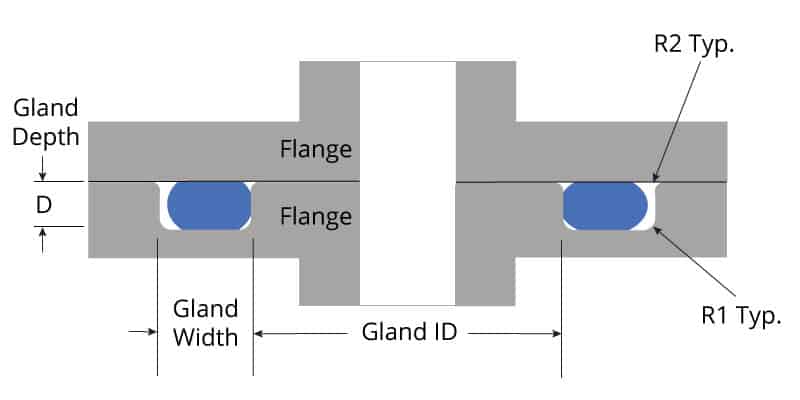



O Ring Groove Design Global O Ring And Seal
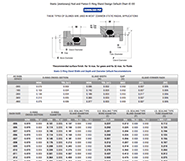



O Ring Groove Design Guides Engineering Quick Reference




O Ring Groove Design Standard As568b Seal Design Inc
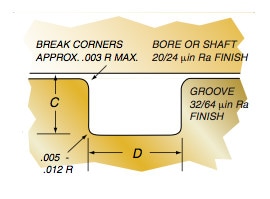



Groove Design Quad Ring Seals Minnesota Rubber Plastics




Mating Ring An Overview Sciencedirect Topics




Oring Ehandbook
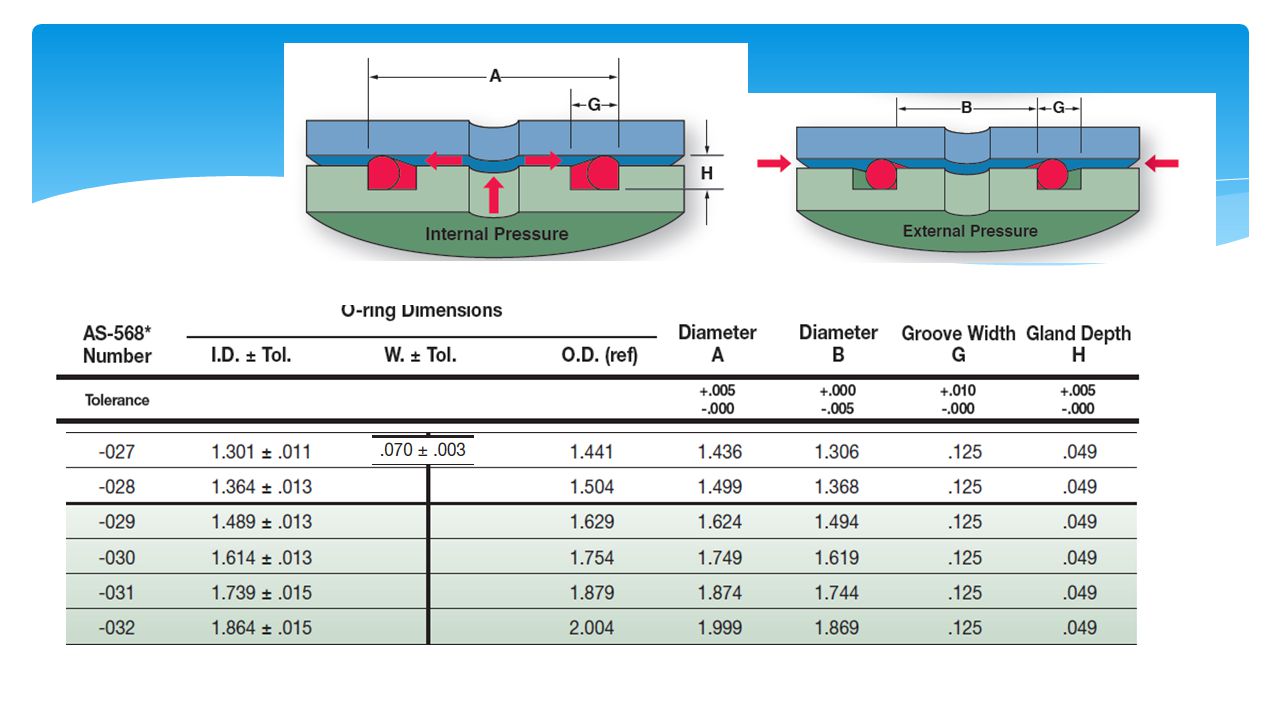



Design Of O Ring Seals Ppt Video Online Download




Buna O Ring O Ring In Houston And Minneapolis Dichtomatik
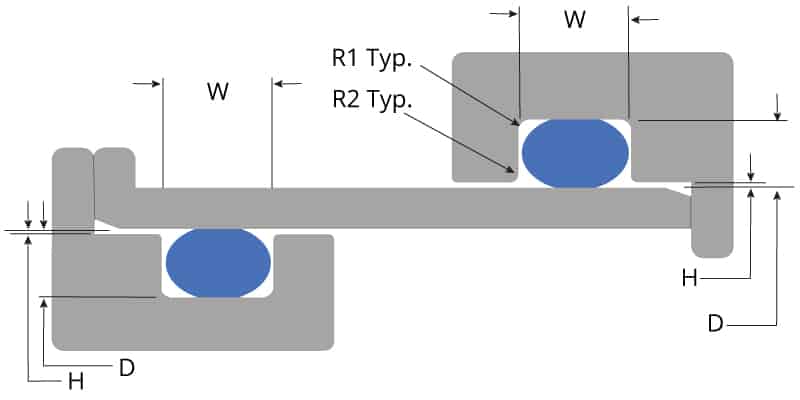



O Ring Groove Design Global O Ring And Seal



1




Oring Ehandbook
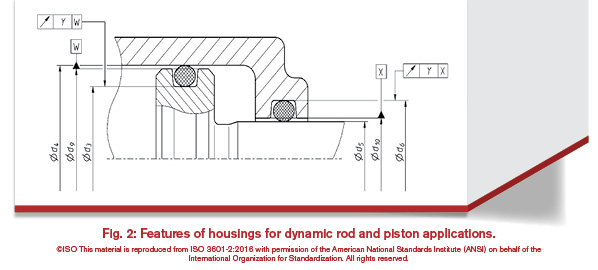



History Of The Iso 3601 Series Of Standards For O Rings Fluid Power Journal
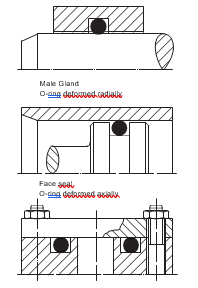



2 Design And Detail Information O Rings Stock O Ring Webshop
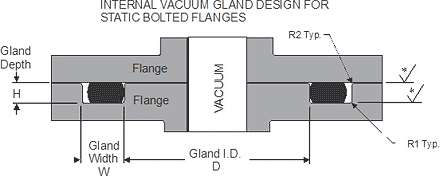



Static O Ring Face Seal Groove Design Guide
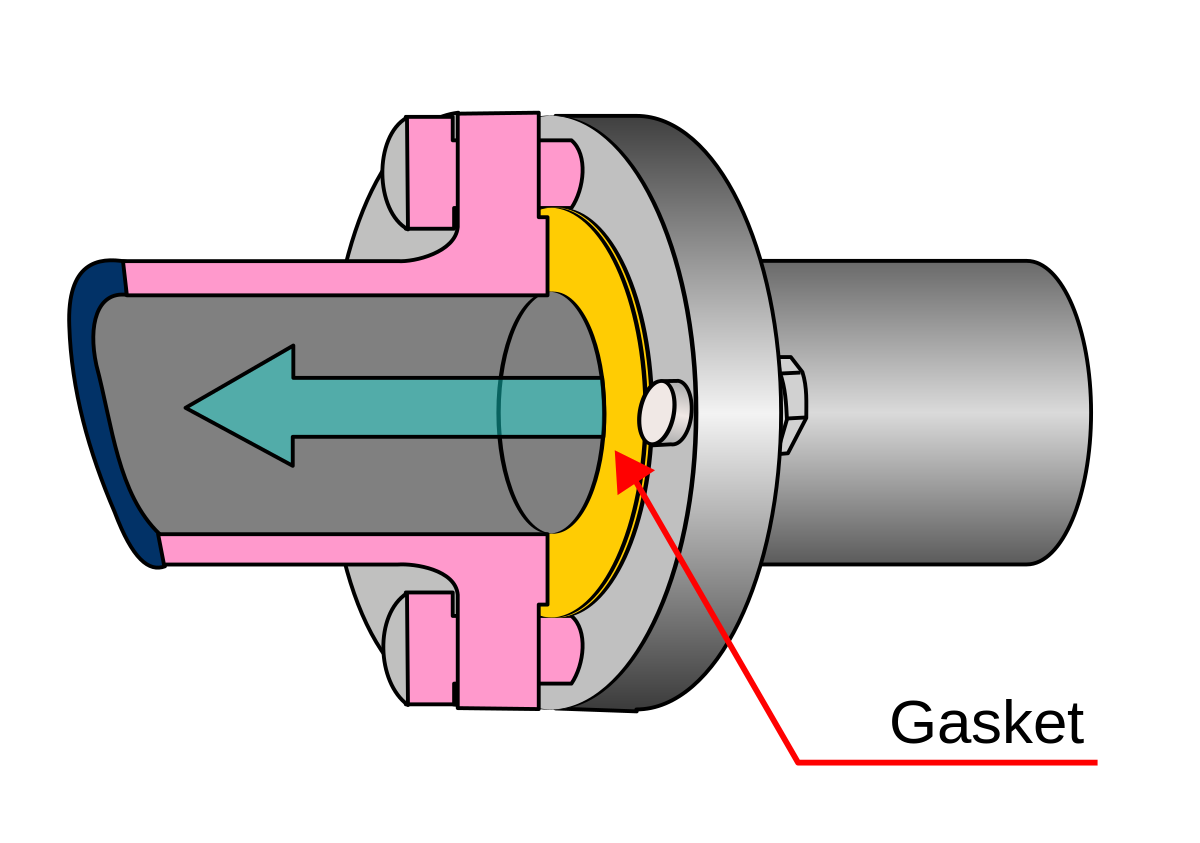



Face Seal Wikipedia
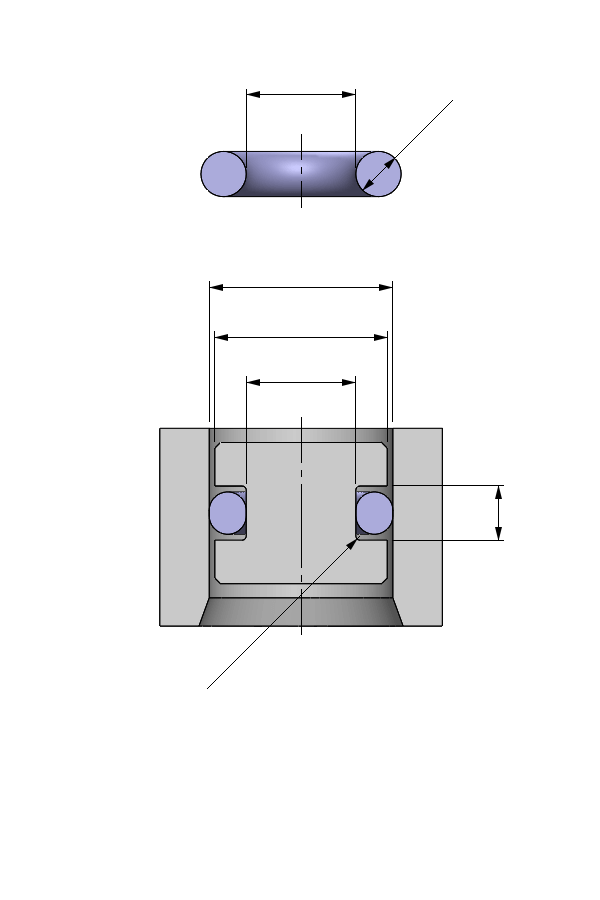



O Ring Calculator Ceetak Sealing Solutions



1




O Ring Grooves



O Ring Groove Design Face Seal




O Ring Groove Design Standard As568b Seal Design Inc
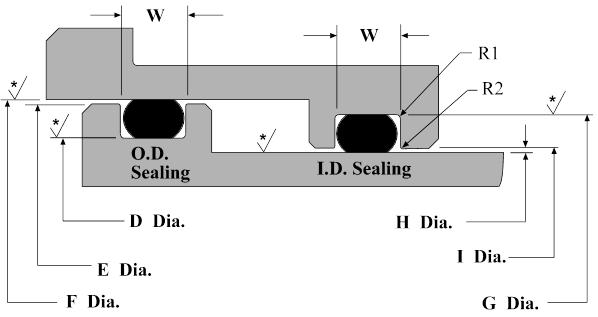



Dynamic O Ring Groove Design Guide A Rod And Piston Glands




Ficient Design Static O Ring Groove Design Mechanical Engineering
0 件のコメント:
コメントを投稿